Measure Corrosion with the 4D InSpec
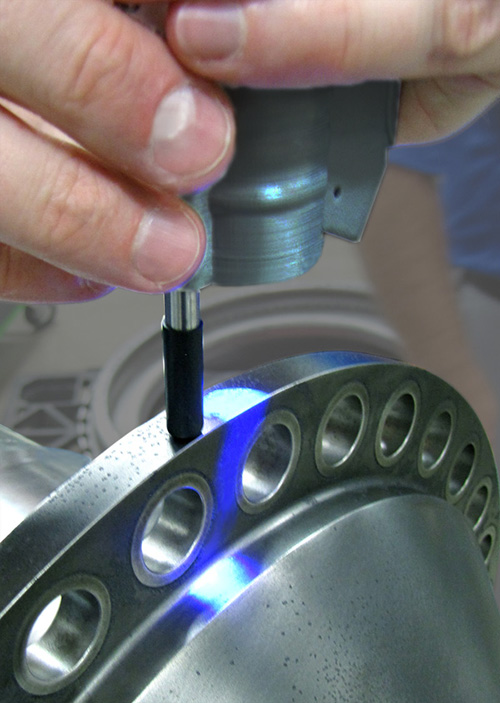
The most used method to measure corrosion is visual inspection. This method is very open to interpretation, however, and operators typically only estimate the depths of what appear to be the most severe features. There is also no established method to estimate the actual area affected by corrosion pits. Lastly, because pit depth measurement is inaccurate inspectors must round up as a safety factor, which frequently leads to scrapping of components which are not necessarily beyond specification.
Nanometer resolution metrology systems can provide more exact, quantitative, 3D corrosion data. These systems, however, are typically too expensive to be affordable for most factory and repair facilities. The systems are typically too susceptible to vibration and noise for shop floor use. They are also most often confined to a measurement stand in a metrology lab, making measurement of large components impractical.
The 4D InSpec Surface Gauge is the first instrument to combine the speed and portability of a handheld gauge with the measurement resolution of much more expensive metrology systems. Unlike a depth gauge, which can assess just one feature at a time, the 4D InSpec instantaneously calculates the depth, width and volume of all pits within the field of view. An inspector can measure many fields of view per minute to quantify large portions of corroded components, providing a thorough and accurate assessment of the severity of corrosion.
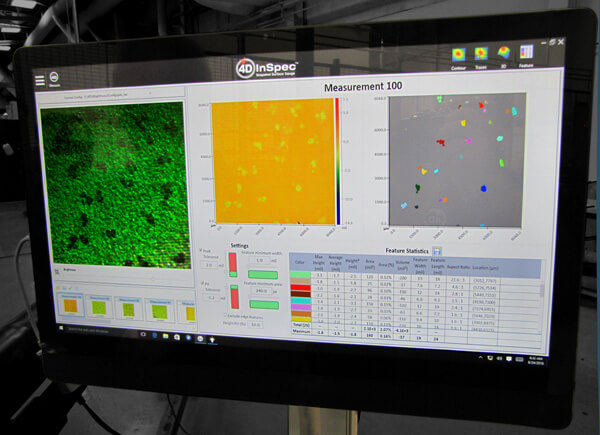
Additionally, an optional fold mirror attachment allows the 4D InSpec to function like a borescope, allowing inspectors to assess corrosion on fillets, on the interiors of pipes, and in other areas without direct line-of-sight.
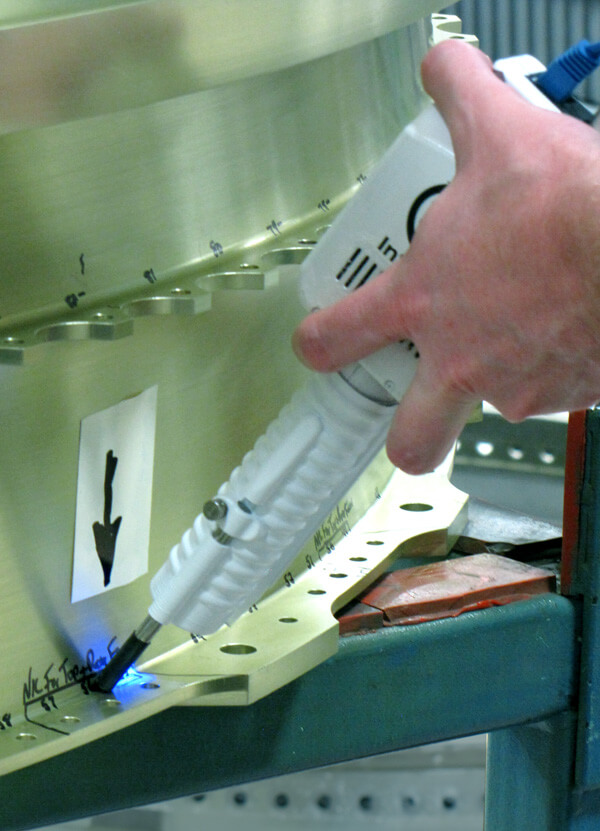
The 4D InSpec Surface Gauge provides a thorough, accurate, repeatable assessment of all the precision surfaces of complex components. With a low purchase price and little ongoing maintenance the gauge makes high resolution measurement affordable for both small and large manufacturing and repair facilities. By fundamentally changing the way companies measure corrosion, the 4D InSpec helps companies properly identify potentially damaging corrosion, as well as avoiding the costly scrapping of expensive components that are truly within specification.
Get In Touch
(520) 294-5600
Location
3280 E Hemisphere Loop, Ste 146
Tucson, AZ 85706
4Dinfo@ontoinnovation.com
Office Hours (Arizona Time)
Mon: 8am - 5pm
Tue: 8am - 5pm
Wed: 8am - 5pm
Thur: 8am - 5pm
Fri: 8am - 5pm
Sat: Closed
Sun: Closed