Aerospace and Aviation
When technicians are able to make accurate, quick, repeatable measurements, that go right up to the specification line, they no longer throw away good parts that they are uncertain–or simply too cautious–about.
When good metrology makes the difference
Aviation and Aerospace parts manufacturing depends on fast turnaround, but never at the cost of safety. The one consistent thing we heard from customers in the field, is that when they started using 4D InSpec, is that the new metrology not only paid for itself many times over, it increased yield.
The status quo is no longer enough
By default, customers in aviation and aerospace are processing parts and making decisions as quickly as possible. In many, many shops, the first line of qualification is a visual comparator, and a fingernail scratch test. For a few, more difficult situations — like when the corrosion is down in a groove that’s too deep and narrow for a fingernail to get into — then the part may be sent to a metrology lab, or perhaps a replica will be taken for analysis.
4D InSpec lets you measure anywhere, and to measure quickly — to literally point and click on the surface, and have a repeatable result in a few seconds. It’s not just an advantage of time, it’s the ability to rely on those results in a way that the metrology lab gives you, without the burden of the lab.
Flightline measurements
Portability can pay off in unexpected ways. Being able to put your metrology in the intake area, or in the disassembly area is certainly a plus. But being able to roll your metrology on a cart over to the engine casing (rather than the other way around) is a huge work-saver.
But go a few steps further: take your inspection gauge, with a tablet for storing and analyzing the data and a battery power supply for reaching without an extension cord… and then inspect parts right on the aircraft, without disassembly.
Yes, you can measure on the tarmac, or in the hangar.
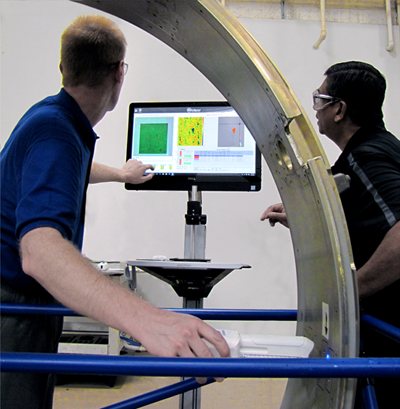
Essential parts inspection
Having to depend on your aircraft’s full performance makes defect inspection during maintenance a mission-critical process. Military engine components and rivets get inspected by 4D InSpec, for fast, repeatable, handheld parts qualification.
Added Technical Resources
Can 4D InSpec replace replica gels?
If you can measure a 3D defect (like an area of corrosion) directly, is there any reason to keep using replications? We examined whether there was correlation between our measurements and the replicas, and found times when replication is still needed. Download the PDF now.
What is 4D InSpec?
This Surface Gauge is the first handheld, high resolution instrument for measuring surface defects and features, right on the factory floor.
Products for Aerospace and Aviation
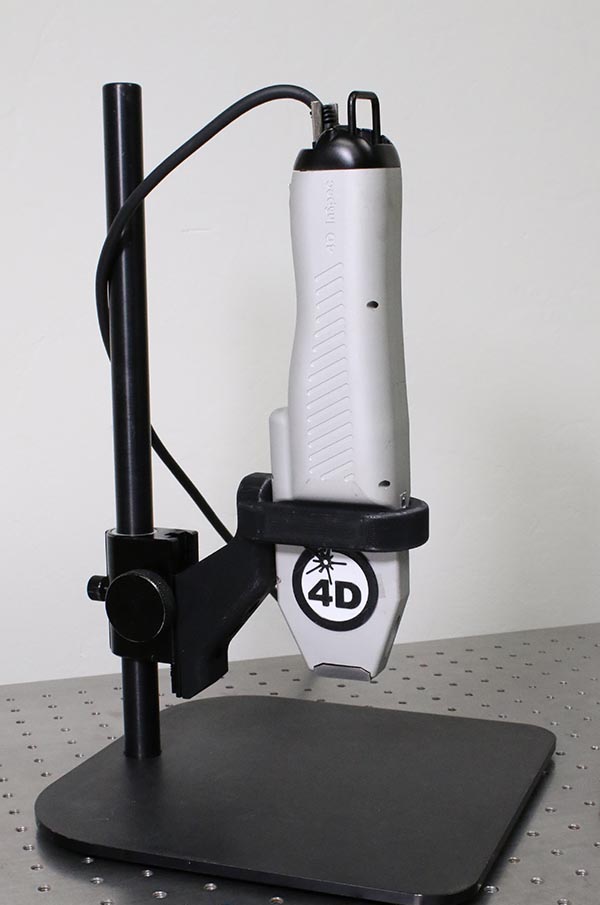
4D InSpec
4D InSpec provides non-contact measurement of surface features and defects, on the factory floor, in machine shops and in field service applications.
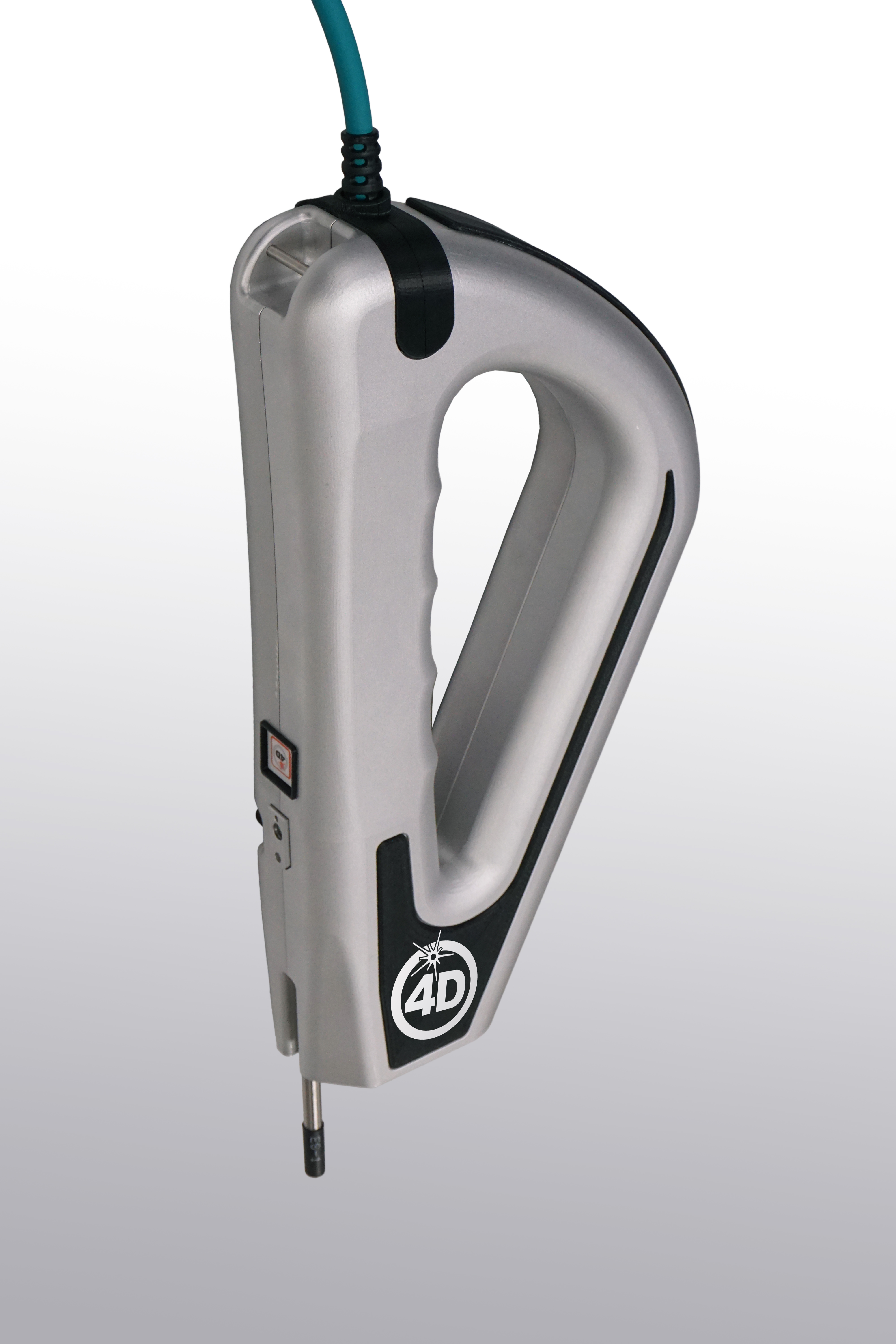
4D InSpec XL
A handheld defect inspection gauge that works like 4D InSpec standard, but with a larger field of view, to measure wider and deeper features.
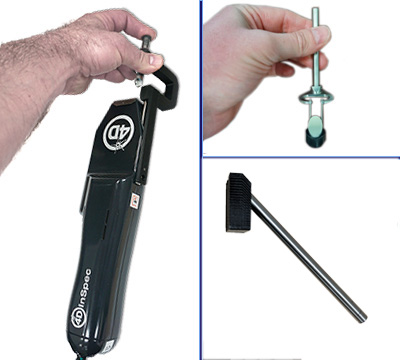
InSpec Accessories
Accessories for improving portability, ease of use, or for accessing hard to reach measurements like sidewalls and through-holes.
Get In Touch
(520) 294-5600
Location
3280 E Hemisphere Loop, Ste 146
Tucson, AZ 85706
4Dinfo@ontoinnovation.com
Office Hours (Arizona Time)
Mon: 8am - 5pm
Tue: 8am - 5pm
Wed: 8am - 5pm
Thur: 8am - 5pm
Fri: 8am - 5pm
Sat: Closed
Sun: Closed