in situ polishing metrology
Accurate shape and roughness feedback guides grinding and polishing operations for both small and large optics. Moving smaller optics between polishing centers and a metrology lab may not prove difficult. With large and very large optics, however, these trips can be time-consuming and extremely risky.
One answer is to install measurement equipment directly into polishing systems, which eliminates material handling and fixturing time. The challenge for in situ polishing metrology, however, is overcoming the air flow, vibration and noise associated with such equipment. The measurement systems must also be very compact, and robust enough to stand up to the vibration and debris in this challenging application.
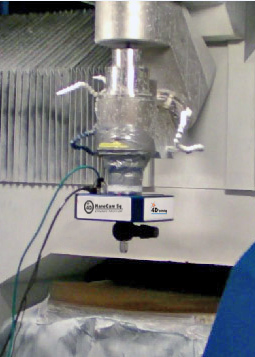
Instantaneous measurement using 4D’s dynamic interferometers and optical profilers makes it possible to measure surface shape (PhaseCam) and surface roughness (NanoCam HD) despite vibration. Both systems have been incorporated directly into polishing equipment, providing immediate feedback for the polishing process on many of the world’s premier telescope and space optics projects.
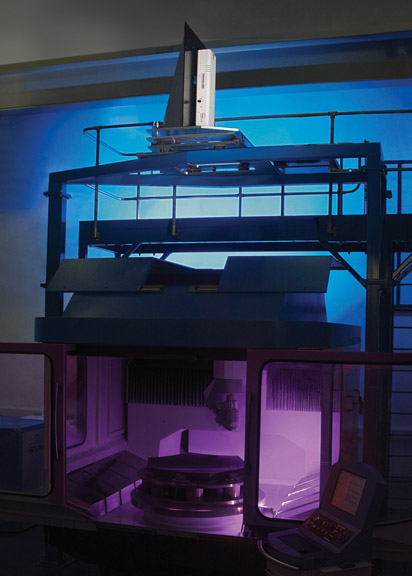
Added Technical Resources
High Throughput Measurement Speeds Production of Large Mirrors
This article discusses the challenges of measuring large optics during polishing, how Dynamic Interferometry
has been applied to overcome these challenges, and the benefits to optics manufacturers of employing the
technique.
Products for In Situ Polishing Metrology
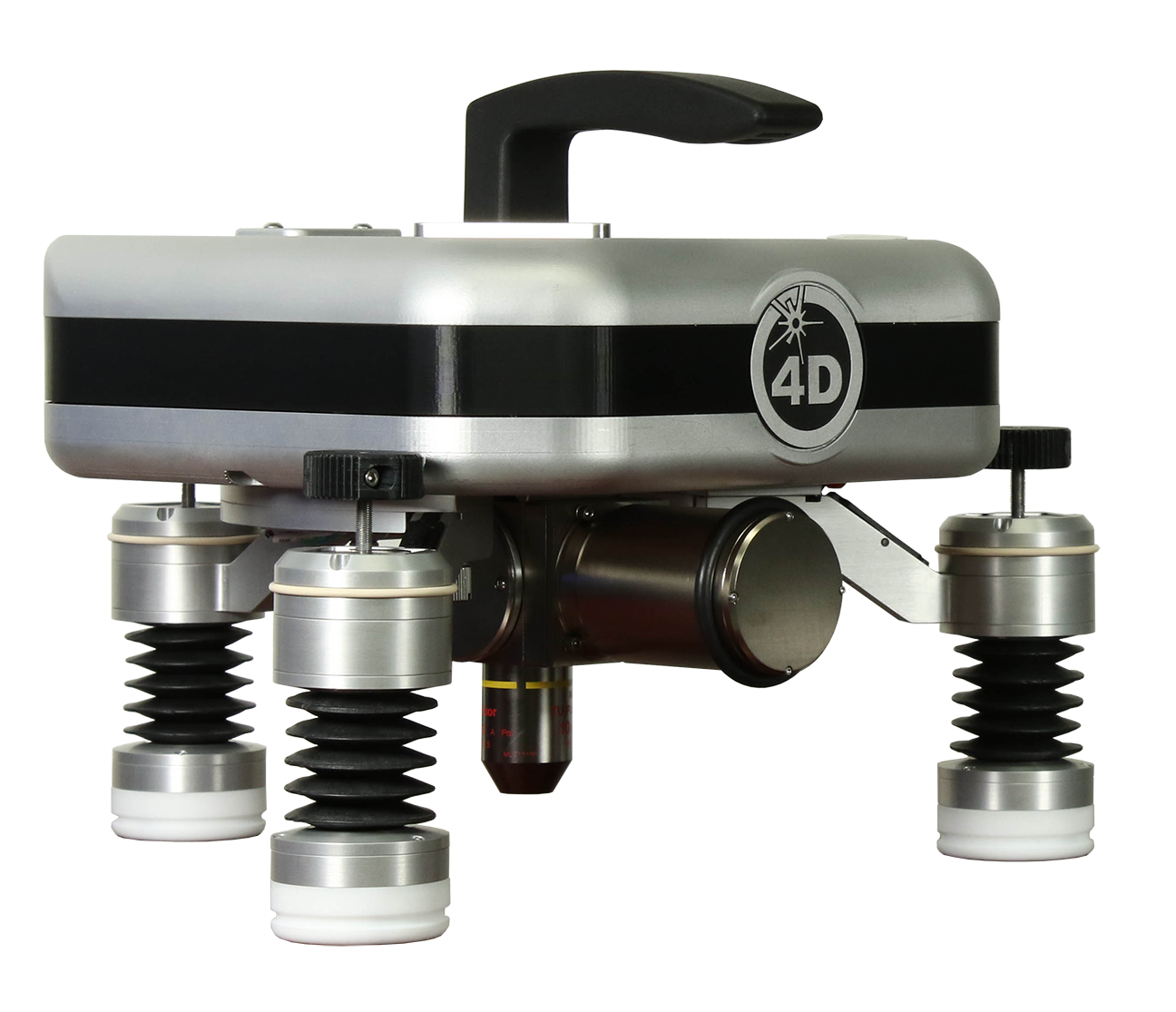
NanoCam HD
NanoCam HD provides shape and roughness feedback throughout the polishing process.
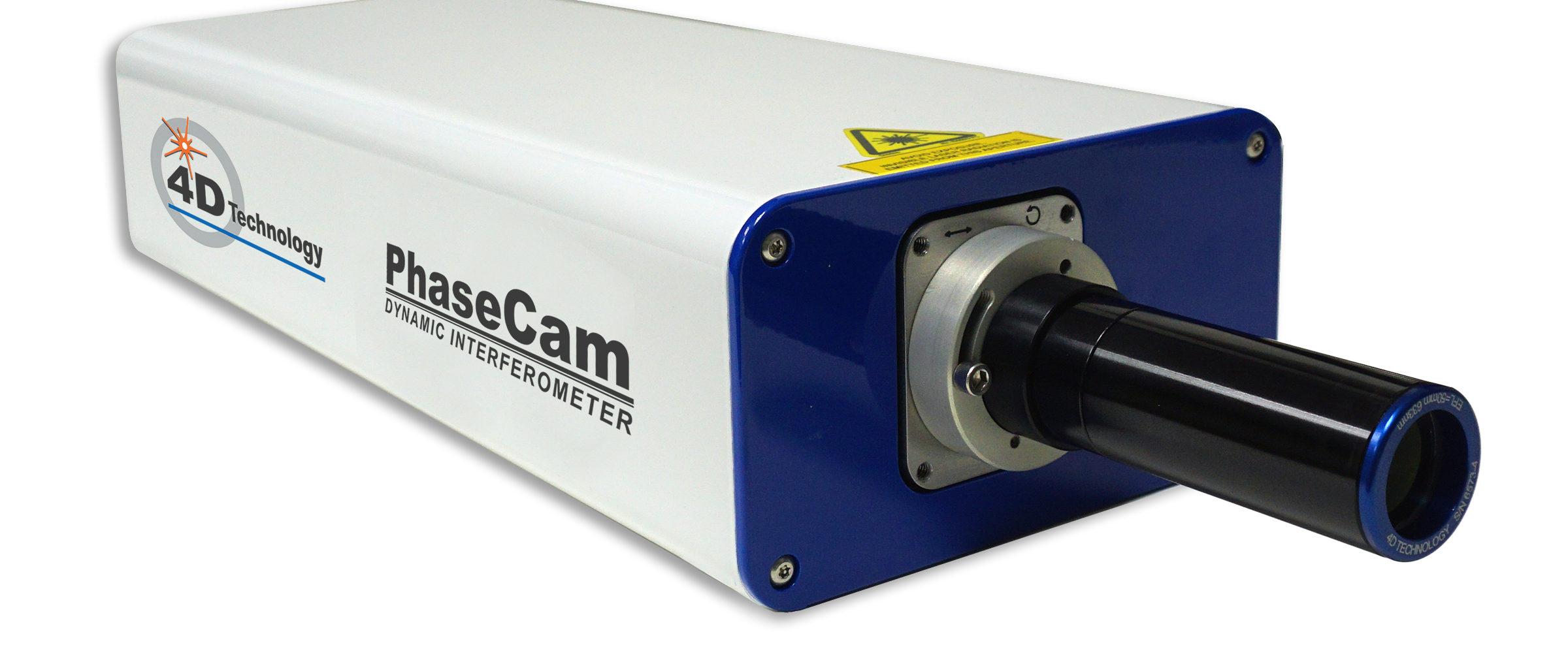
PhaseCam
4D PhaseCam Twyman-Green interferometers are the industry choice for measuring concave spherical optics, from several millimeters to tens of meters in diameter.
Get In Touch
(520) 294-5600
Location
3280 E Hemisphere Loop, Ste 146
Tucson, AZ 85706
4Dinfo@ontoinnovation.com
Office Hours (Arizona Time)
Mon: 8am - 5pm
Tue: 8am - 5pm
Wed: 8am - 5pm
Thur: 8am - 5pm
Fri: 8am - 5pm
Sat: Closed
Sun: Closed